Polymer flooring in the garage
We arrange polymer flooring in the garage – the nuances of the choice of materials, the basics of installation techniques
What car owner would refuse to equip his garage so that the premises are safe, reliable in operation, and even look aesthetically pleasing? At the same time, I would like to allocate a minimum of time to maintain cleanliness, and forget about repair work for many years. Polymeric garage flooring is the desired root of this equation with many unknowns.
A polymer self-leveling floor in a garage must cope with an impressive set of serious challenges:
- withstand high specific pressure;
- have an impressive impact resistance;
- resist cracking regardless of temperature and humidity surges;
- characterized by high wear resistance;
- not be afraid of aggressive chemical environments;
- be resistant to dirt and easy to clean;
- have a presentable appearance;
- provide fire safety.
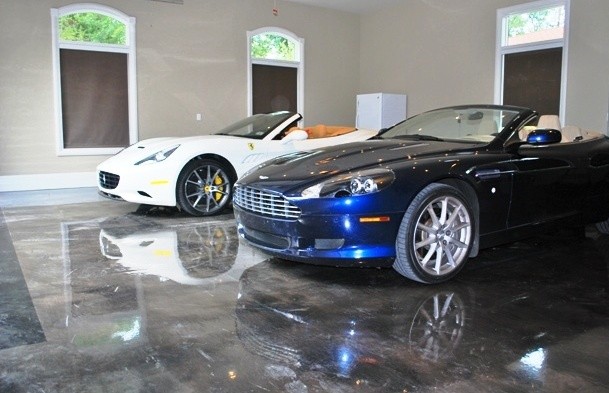
For many years, porcelain stoneware was considered the most popular material in this area. True, there was a problem with it about the impact strength: it is fragile, it may well crack from a heavy metal object that has fallen from a height of 1 – 1.5 m (for example, a wrench). Yes, and the glue layer often let down, which is why periodically it was necessary to cut down individual tiles and replace them with new ones. Another significant drawback of this material is that it is too slippery when polished, and it is very difficult to remove oil stains from rough tile types.
Modern building polyurethanes and epoxy resins are devoid of all of these disadvantages. It is from these components in various combinations that the flooded floor in the garage is made, which meets all the requirements from the above list.
Epoxy mixtures differ from polyurethane compounds in higher strength and hardness, but affordable resin brands cannot be simultaneously resistant to chemistry and abrasion. But polyurethane combines the last two qualities at a high level. Therefore, the most common option for a garage floor sandwich is an epoxy base with a urethane varnish on top.
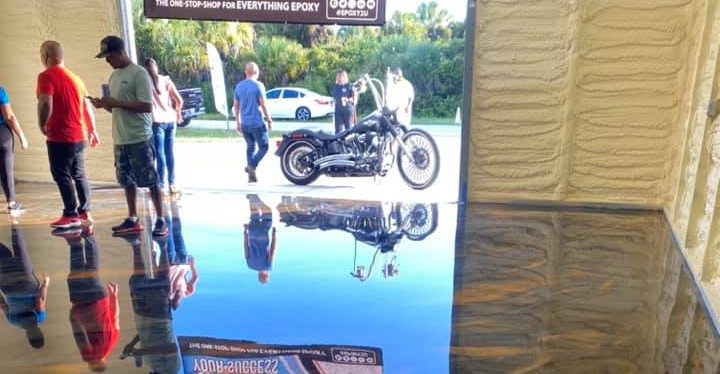
Earthworks and redevelopment
Polymer coating technology for garage floors
Depending on the condition of the concrete screed, the expected level of specific pressure on the surface and aesthetic requirements, 3 basic installation schemes are used:
- Polyurethane floor.
- Epoxy base with urethane varnish.
- Epoxy resin, quartz filler and urethane varnish.
To figure out which self-leveling floor is optimal for a particular garage, consider the pros and cons of each wiring diagram.
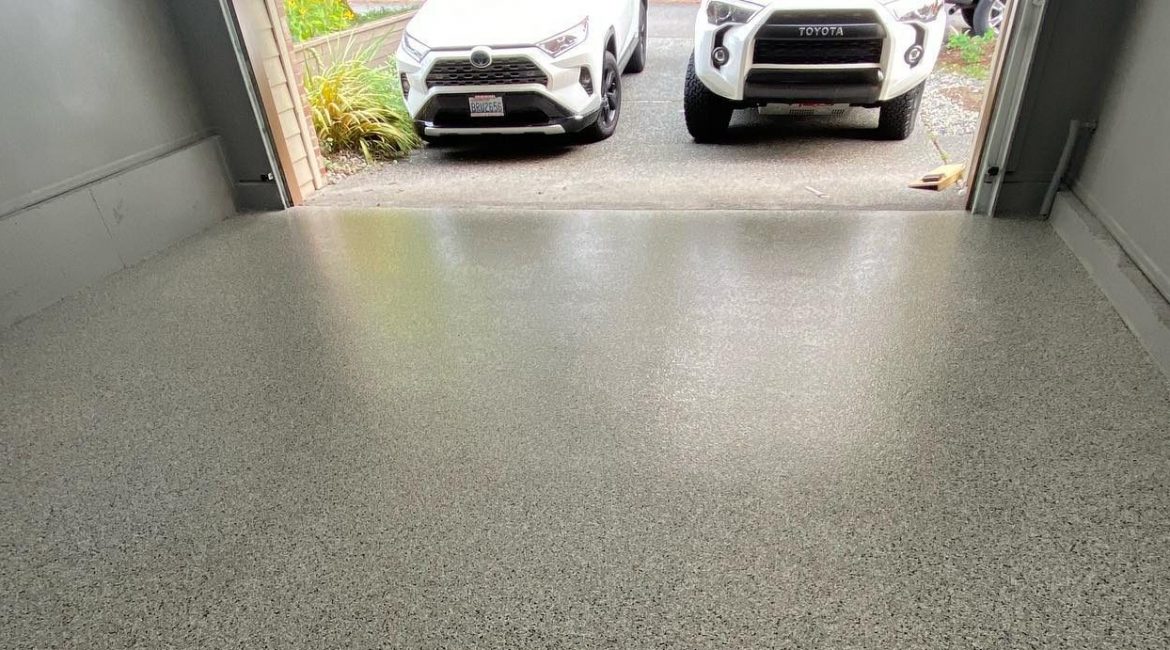
Epoxy base with urethane varnish
Perhaps the most popular scheme at the moment. Colored acrylic flocks (chips, flakes) are added to the uncured epoxy layer, and then, after complete drying and mechanical treatment, the surface is hidden with urethane varnish.
The technology is suitable for private garages for any class of cars. To achieve high quality and a long service life, you should choose base materials from reputable companies in the field of industrial flooring.
The main criteria for choosing the type of polymer floor for a garage are the requirements for surface strength (level of permissible specific pressure) and decorative properties of the coating. The rest of the quality indicators – from shock resistance to fire safety – are fully ensured with all the considered installation schemes.
The main activity of the company is :
- building of the garages, hangars,
- epoxy floors, polishing of the concrete, industrial floors painting
- residential remodeling,
- building of decks, porches and stairs